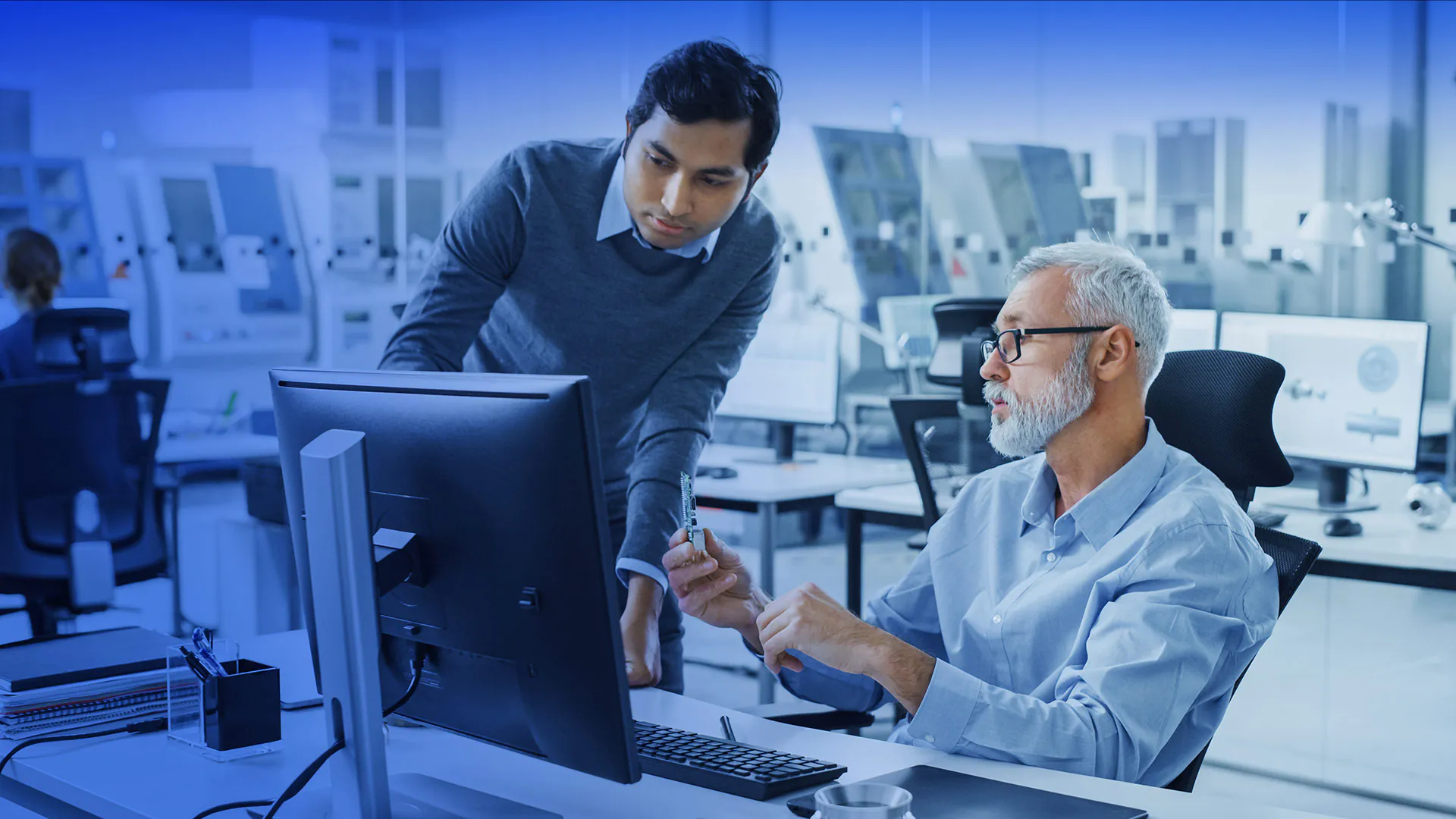
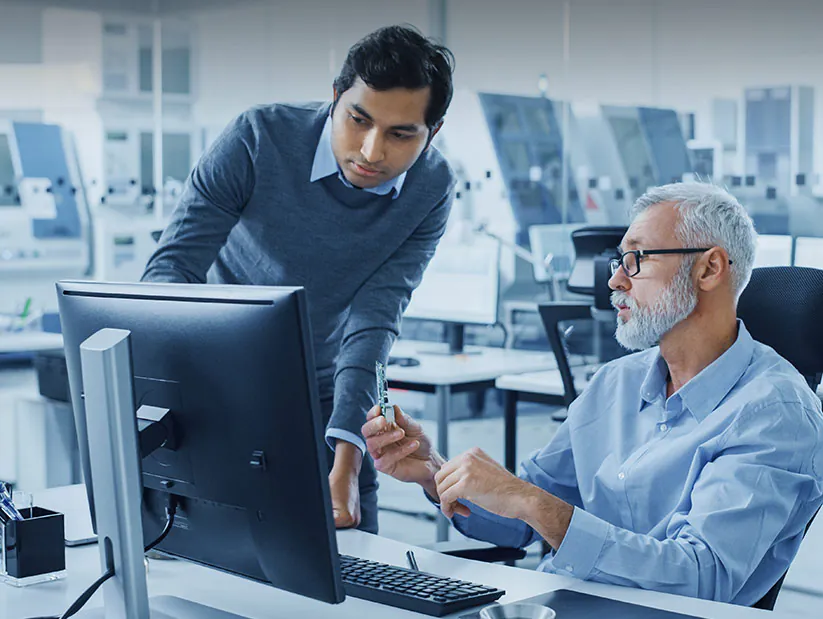
Case Study
Warehouse Transformation at leading supplier of spare parts for garden supplies
Stabilization of stocking and warehousing processes required
Company details
- Sales EUR 42.5 million, parent company sales EUR 128 million, group worldwide approx. USD 1.4 billion (2021). Takeover (sales EUR 217 million) planned for September 2022.
- Number of employees: 125; parent companies in Europe: 381 (09/22); part of a private equity company
Situation and Challenge
- Stabilization of stocking and warehousing processes required
- Lack of process and workflow descriptions (impeding ERP change)
- Data availability and data quality very poor, which, among other things, makes quick analysis of day-to-day business difficult
Objective and Task
- Warehouse transformation (organization, processes and technology)
- Preparation, support and assurance of ERP change within the area of responsibility
- Head of on-site logistics (staff responsibility for 58 employees)
Measures and Procedures
- Analysis and development of various business and system concepts, process and flow descriptions in connection with planned ERP changeover.
- Execution of large number of test cases during run-up (pre go-live, cut-over) and in the aftermath (Hypercare phase) of the ERP change (including all interfaces to logistics) Observation, evaluation and implementation of various process and workflow improvements
Results and Achievements
- Complete assurance and implementation of the ERP change by go-live date.
- Execution of a key date inventory in record time (half the time of previous year)
- Definition of performance criteria as well as introduction of logistics reporting with the aim of measuring and optimizing processes and activities (also for European group of companies)
Case Study
Project Manager New Buildings
A high-tech producer is expanding due to strong growth with a new headquarters and logistics center. The project manager coordinates the new building and reconstruction work within the budget and time frame, ensures continuous delivery capability and selects suitable warehouse technology. The milestones were …
Case Study
Taskforce Manager Front Camera
An Atreus front camera taskforce leader at a globally active French Tier 1 supplier overcame leadership and process problems in the front camera project. By restructuring the core team, introducing agile methods and team building measures, development cycles were shortened and customer satisfaction increased.
Case Study
Overall Project Manager Autonomous Shuttle
An Atreus overall project manager for the subsidiary of a German Tier 1, successfully carried out the retrofit of the object recognition system of autonomous shuttles in the Netherlands. The project was completed on time, with improved driving behavior and successful handover to the …